- РЕЗЦЫ ТОКАРНЫЕ ПРИЗМАТИЧЕСКИЕ. ТЕРМИНЫ И ПРЕДЕЛЕНИЯ
- ЧАСТИ РЕЗЦА
Резец (рис.1) состоит из рабочей части (головки) 1 и державки (корпуса) 2.
Рабочая часть непосредственно осуществляет процесс резания. Державка служит для установки и закрепления резца в станке.
Рис.1. Части резца
1.2.ЭЛЕМЕНТЫ РАБОЧЕЙ ЧАСТИ РЕЗЦА
Рабочая часть резца (рис.2) состоит из следующих элементов:
- передней грани 1 - поверхности, по которой сходит стружка;
- задних граней 2 и3 - поверхностей, обращенных к обработанной поверхности заготовки;
- режущих кромок - линий пересечения передней и задних граней; режущие кромки разделяются на главную режущую кромку 4, выполняющую основную работу по снятию припуска, и вспомогательную режущую кромку 5, выполняющую калибрование и зачистку обработанной поверхности; резцы могут иметь одну (например, проходные) или две (например, отрезные) вспомогательные режущие кромки; задняя грань, образующая главную режущую кромку, называется главной задней гранью, а вспомогательную режущую кромку - вспомогательной задней гранью;
- вершины резца 6 - места сопряжения главной и вспомогательной режущих кромок;
- высота головки резца h (рис.3) - расстояние от вершины резца до опорной поверхности;
- длины головки резца l - расстояния от вершины резца до выхода поверхности заточки;
- оси резца 2 - совокупности точек пересечения осей симметрии поперечных сечений державки резца.
1.3. ТИПЫ РЕЗЦОВ
Наиболее полная классификация резцов приведена в работе [3]. В большинстве случаев понятие типа резца достаточно полно раскрывается самими наименованными признаков и типов. Поэтому рассмотрим определение типов резцов лишь по двум признакам:
а) по направлению подачи:
-правые резцы работают при подаче справа налево, в направлении шпинделя; при наложении ладони правой руки сверху главная режущая кромка располагается со стороны большого пальца;
-левые резцы работают при подаче слава направо; при наложении ладони левой руки главная режущая кромка располагается также со стороны большого пальца;
б) по конструкции рабочей части:
-прямые резцы, у которых ось резца - прямая линия;
-обогнутые резцы, у которых ось резца на виде в плане имеет форму кривой или ломаной линии; у правых отогнутых резцов головка отогнута влево, у левых - вправо;
-изогнутые резцы, у которых ось резца имеет также криволинейную форму, но уже в другой плоскости - на виде сбоку;
-оттянутые резцы, у которых ширина головки меньше ширины державки; головка может быть расположена как по оси резца, так и сдвинута параллельно ей вправо или влево, соответственно, резцы будут называться вправо оттянутыми или влево оттянутыми.
1.4. ПОВЕРХНОСТИ И КООРДИНАТНЫЕ ПЛОСКОСТИ
При обработке токарными резцами на заготовке различают следующие поверхности (рис.4): обрабатываемую поверхность 1, поверхность главного движения 2 и обработанную поверхность 3.
Обрабатываемой называют поверхность, с которой предстоит снимать припуск. Обработанная поверхность образуется в результате снятия припуска после прохода резца. Поверхностью главного движения называют поверхность, которая образуется режущей кромкой в результате главного движения заготовки, т.е. это переходный участок между обрабатываемой и обработанной поверхностями.
Для определения в процессе резания положения поверхностей, образующих режущую кромку, используют две координатные плоскости. Основная плоскость проходит через рассматриваемую точку режущей кромки перпендикулярно направлению скорости главного движения резания. На резце основная плоскость 5 (рис.4) является установочной базой. Плоскость резания - это координатная плоскость, касательная к режущей кромке в рассматриваемой точке и перпендикулярная основной плоскости.
1.5. УГЛЫ РЕЗЦА
При конструировании резца угловые размеры рабочей части проставляются относительно координатных плоскостей. При этом принимается, что резец на станке устанавливается вершиной по центру заготовки, а ось его перпендикулярна линии центров (обработка наружных поверхностей).
Углы резца г, б, в и д , измеренные в главной секущей плоскости А-А (рис.4), называются главными. Плоскость А-А перпендикулярна к проекции главной режущей кромки на основную плоскость.
Главным передним углом г называется угол, образуемый линиями (проекция А-А): следом сечения передней грани и следом сечения плоскости, проходящей через режущую кромку параллельно основной, плоскости.
Главным задним углом б называется угол между следом сечения главной задней грани и следом сечения плоскости перпендикулярной основной плоскости.
Главным углом заострения в называется угол между следом сечения передней поверхности и следом сечения главной задней грани.
Углом резания д называется угол между следом сечения передней грани и следом сечения плоскости перпендикулярной основной плоскости.
Вспомогательные углы измеряются во вспомогательной секущей плоскости Б-Б, которая перпендикулярна проекции вспомогательной режущей кромки на основную плоскость. Например, вспомогательный задний угол б1 (проекция Б-Б) образуется между следом сечения вспомогательной задней грани и следом сечения плоскости перпендикулярной основной плоскости.
Углы в плане ц и ц1 обозначены на виде резца сверху (в плане).
Главным углом в плане ц называется угол между проекцией главной режущей кромки на основную плоскость и направлением рабочей подачи,
Вспомогательным углом в плане ц1, называется угол между проекцией вспомогательной режущей кромки на основную плоскость и направлением подачи.
Углы наклона режущих кромок л и л1 обозначены на видах В и Г.
Углом наклона главной режущей кромки л называется угол между главной режущей кромкой и плоскостью, проходящей через вершину резца параллельно основной плоскости.
Углом наклона вспомогательной режущей кромки л1 называется угол между вспомогательной режущей кромкой и плоскостью, проходящей через вершину резца параллельно основной плоскости.
Угол л считается положительным, если все точки режущей кромки располагаются выше вершины резца, и отрицательным, если - ниже вершины резца. Дня угла л1 условия определения знаков изменяются на противоположные.
2. ВЛИЯНИЕ ГЕОМЕТРИЧЕСКИХ ПАРАМЕТРОВ НА РЕЖУЩУЮ СПОСОБНОСТЬ РЕЗЦА [3]
Процесс резания металлов относится в технике к числу наиболее сложных. Условия его протекания зависят от большого количества факторов: свойств материалов инструмента и заготовки, размеров срезаемого слоя, режим резания, состояния технологического оборудования и др. Все эти факторы оказывают воздействие на режущую способность резца, создавая нагрузки на передней и задней поверхностях лезвия, близкие к разрушающем» контактную температуру, близкую к теплостойкости инструментального материала, силы трения и вибрации различной интенсивности. Воздействие указанных факторов на резец и качество обработанной поверхности изменяется в зависимости от значений геометрических параметров рабочей части резца, причем, каждый параметр оказывает как прямое, так и косвенное влияние. Наличие большого числа воздействующих факторов и их сложной связи с процессом резания не позволяют иметь надежные рекомендации значений геометрическое параметров для всех случаев практики. Поэтому рассмотрим принципиальные положения, которыми следуем руководствоваться при конструировании режущей части резцов различных типов.
Задний угол. Изменением заднего угла можно регулировать контактное давление на заднюю грань резца со стороны упруго деформированного материала заготовки за линией среза. Задний угол оказывает влияние на точность формы, размеров я качество обработанной поверхности. Путем изменения заднего угла достигают снижение силы резания, повышают прочность режущей кромки, увеличивают её износостойкость. В зависимости от толщины срезаемого слоя задний угол следует выбирать согласно табл.1.
Таблица 1
Значения задних углов резца, град.
Тип резца
|
Толщина среза
|
менее 0,2 мм
|
более 0,2 мм
|
Проходные, подрезные
Отрезные, прорезные
Расточные
|
12
12-15
12-15
|
6-8
8-10
8-10
|
Задняя поверхность резца должна быть выполнена так, чтобы затраты на заточку были минимальными. Технологичным считается такое конструктивное решение, при котором задняя поверхность подвергается обработке лишь на небольшой ширине вблизи режущей кромки. Это достигают за счет соответствующего угла врезания пластины. Вспомогательный задний угол принимается равным главному заднему углу.
Передний угол. Основное назначение переднего угла - уменьшение деформации стружки и обработанной поверхности. От величины переднего угла зависит величина и направление силы резания, соотношение растягивавших и сжимающих напряжений в режущем клине, температура, интенсивность вибрации и в итоге износостойкость резца.
У твердосплавных резцов передний угол в зависимости от свойств материала заготовки может иметь положительное или отрицательное значение. Передняя поверхность выполняется плоской или криволинейной. Плоская форма применяется для обработки хрупких и высокотвердых материалов, криволинейная - для обработки вязких материалов низкой и средней твердости. Обе формы могут включать ленточку вдоль режущей кромки шириной f = 0,2 - 1,0 мм в зависимости от величины подачи. У резцов из быстрорежущей стали передний угол на ленточке положительный г1=50-80, у твёрдосплавных - отрицательный от -30 до -100 . Ленточка предохраняет режущую кромку от выкрашивания. При работе с малыми толщинами среза (менее 0,25 мм) ленточку не применяют, но предусматривают возможность притупления режущей кромки оселком до 0,2 мм. Криволинейная форма передней поверхности обеспечивает дробление или
завивание сливной стружки.
Угол наклона главной режущей кромки. Основное назначение угла л - обеспечить заданное направление схода стружки, получить обработанную поверхность требуемого качества, повысить прочность резца. При отрицательном угле л стружка свободно сходит с передней поверхности в направлении от заготовки (рис.5а) и не соприкасается в дальнейшем с обработанной поверхностью. Для резца с положительным углом л направление схода стружки при свободном резании изменяется на противоположное (рис.56). При несвободном резании (рис.5в) стружка у корня подвергается дополнительной пластической деформации и принудительно изменяет направление схода или скалывается. В результате воздействия стружки шероховатость обработанной поверхности возрастает. В условиях автоматизированного производства управление сходом стружки приобретает первостепенное значение [4].
Главный угол в плане. Угол ц через изменение соотношения между шириной и толщиной среза (при постоянных значениях подачи и глубины резания) оказывает влияние на радиальную Рy и осевую Рx составляющие силы резания, интенсивность вибраций, износостойкость резца. При обработке нежёстких заготовок угол ц увеличивают до 90°. Если жёсткость заготовки не является лимитирующей, то угол ц уменьшают до 10 - 20° при чистовой обработка и до 30 - 45е - при черновой.
Вспомогательный угол в плане. Основным назначением угла ц1 является обеспечение условий калибрования и зачистки обработанной поверхности. Угол ц1 влияет на шероховатость обработанной поверхности, прочность вершины и износостойкость резца. С уменьшением ц1 его положительное влияние на указанные факторы возрастает. При достаточной жесткости и виброустойчивости упругой и динамической систем станка угол ц1 принимают равным 10 - 15°. При работе с врезанием угол ц1 увеличивают до 20 - 30°. Из опыта работы токаря-новатора В.А.Колесова (1053г.) известно, что применение дополнительной вспомогательной кромки с углом цg=00 позволяет применять додачу в пределах 2 - 12 мм/об при чистовой и получистовой обработке.
Радиус вершины резца. Главная и вспомогательная режущие кромки сопрягаются на вершине дугой окружности радиуса r. Влияние его на работу резца аналогично углу ц1. С увеличением радиуса вершины резца повышается износостойкость инструмента и снижается шероховатость обработанной поверхности. Вместе с тем увеличение радиуса r сопровождается увеличением составляющих силы резания Рz и Ру при уменьшении Рx,т.е. радиус оказывает на силу резания такое же влияние, как и угол ц1. С учетом указанных факторов радиус вершины токарных резцов принимают в пределах 0,5 - 3 мм. Увеличение радиуса возможно при отсутствии действия ограничений по жесткости и виброустойчивости.
3. РАСЧЕТ НАЛАДОЧНЫХ УГЛОВЫХ РАЗМЕРОВ ДЛЯ ЗАТОЧНЫХ ОПЕРАЦИЙ
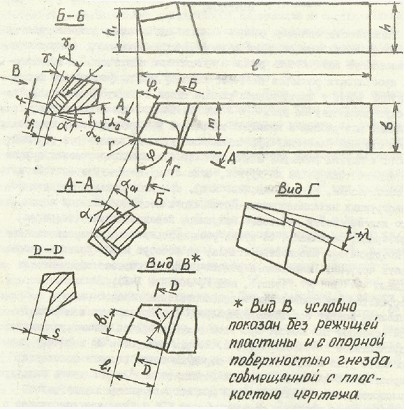
При конструировании резцов принято проставлять угловые размеры рабочей части относительно координатных плоскостей, совмещая установочную поверхность резца с плоскостью чертежа. Такая система простановки размеров отвечает ванному принципу общности формы режущей части у инструментов разных типов и поэтому имеет практическую ценность. На рис. 6 и 7 приведены примеры конструктивных решений для резцов с напайной пластиной и с механическим креплением сменной пластины. При совпадении угловых параметров режущей части и других размеров можно принять обоснованное решение о замене одного типа резца на другой, если этому не будут препятствовать экономические, организационные и др. причины. Однако в целом обе конструкции нетехнологичны. Нетехнологичностъ выражается в том, что для обработки на станке, например, передней грани (операции фрезерная, заточная), её нужно установить в положение, совмещенное с координатной плоскостью станка, за которую можно принять плоскость чертежа. Положение передней грани на чертеже определяется углами л и г (рис.6, вид Г, сечение Б-Б). Предположим, что посредством двухповоротного приспособления поворот на угол л выполнен вокруг оси перпендикулярной режущей кромке и параллельной основной плоскости. При этом режущая кромка займет положение параллельное плоскости чертежа. Вторым поворотом на величину двугранного угла можно выставить переднюю грань резца в положение, параллельное плоскости чертежа (стола станка), и закончить наладку приспособления. Однако нужный для второго поворота двугранный угол не равен главному переднему углу г, так как расположен в другой секущей плоскости. Возникает необходимость определения этого двугранного угла. Кроме того, даже если этот угол вычислить, то базирование резца по режущей кромке оказывается задачей трудно - выполнимой. На практике данную технологическую задачу принято решать в два этапа: 1. Определить углы режущих кромок в двух ортогональных сечениях - продольном и поперечном (рис.8). 2. Определить угловые наладочные размеры приспособления на заточной операции.

3.1 ОПРЕДЕЛЕНИЕ УГЛОВ РЕЖУЩИХ КРОМОК В ПРОДОЛЬНОМ И ПОПЕРЕЧНОМ СЕЧЕНИЯХ
Расчетные формулы для определения углов в продольном и поперечном сечениях (рис.8) получены методами тригонометрии [3] и векторной алгебры [5]:
3.2. ОПРЕДЕЛЕНИЕ НАЛАДОЧНЫХ УГЛОВЫХ РАЗМЕРОВ ДЛЯ ОБРАБОТКИ ПЕРЕДНЕЙ ГРАНИ РЕЗЦА
Наладка приспособления состоит в осуществлении двух последовательных поворотов резца в продольном и поперечном сечениях в координатной системе станка XYZ так, чтобы в результате передняя грань заняла положение, параллельное координатной плоскости станка XOY (рис.9).
Эти углы гпр и гпоп определены формулами (1,2), но в координатной системе резца OXYZ. При наладке первый поворот резца выполняется на угол гпоп вокруг совмещенных осей X и Х' (проекция А-А). Следующий поворот выполняется в плоскости продольного сечения резца гпр , но резец вместе со своей координатной системой уже повернут на угол гпоп (O'Х'Y'Z')и ось поворота у приспособления OY уже не совмещена с осью резца OY'. Возникает задача определения величины угла г'пр второго поворота вокруг оси OY в координатной системе станка. Искомый угол г'пр определен графическим путем и показан на проекции (видБ).
Из рассмотрения прямоугольных треугольников ado (проекция А-А), aco и bco (проекция вид Б) следует:
3.3 ОПРЕДЕЛЕНИЕ НАЛАДОЧНЫХ УГЛОВЫХ РАЗМЕРОВ ДЛЯ ОБРАБОТКИ ГЛАВНОЙ ЗАДНЕЙ ГРАНИ РЕЗЦА
Наладка приспособления состоит в осуществлении двух последовательных поворотов резца: в поперечном сечении на угол бпоп и в плоскости ХОY на главный угол в плане ц' (рис.10) так, чтобы в результате задняя главная грань совместилась c координатной плоскостью YOZ станка.
Углы бпоп и ц заданы в координатной системе резца OX'Y'Z'. При наладке первый поворот резца выполняется на угол бпоп (4) вокруг совмещенных осей X и X'. Следующий поворот следует выполнять вокруг оси OZ, но резец со своей координатной системой OX'Y'Z' уже повернут на угол бпоп так, что главная режущая кромка изменила свое первоначальное положение на новое, заданное углом ц'?ц. Возникает задача определения угла поворота ц'вокруг оси станка OZ.
Решение задачи определения угла ц' выполним на основе метода точечного преобразования координат [8]. Порядок преобразования координат при переходе от новой системы OX'Y'Z', в которой задан резец после поворота на угол бпоп, к старой системе координат станка OXYZ приведен в табл.2.
Порядок преобразования координат
Переход совершается
|
Ось перехода
|
Величина перехода
|
Матричная форма записи
|
от системы
|
к системе
|
OX'Y'Z'
|
OXYZ
|
OX'
|
бпоп
|
X=ATX'
|
В подробной записи
Формулы преобразования получают вид
X=X'; Y=COS бпопY'+SIN бпопZ'. (17)
Координаты точки М на главной режущей кромке в новой системе OX'Y'Z' (рис.10):
X'=COSл SINц; Y'= -COSл COSц; Z'= SINл
Координаты той же точки М' в старой системе координат определяются после подстановки X',Y',Z' в (17)
X=COSл SINц; Y=-COS бпоп COSл COSц+SIN бпоп SINл (18)
Искомый угол ц' определяется формулой tg ц'=X/Y или после подстановки значений и преобразования с учетом знака угла ц по определению
(19)
Поворотом резца на угол ц? завершается настройка приспособления для заточки главной передней грани.
Проверка формулы. Исходные данные: б = 5?; ц = 75?; л = 5?; постановка в (4) даёт бпоп = 5,164852?. Подстановка исходных данных (91)
tgц ? = или
ц?= arctg 3, 865374 = 75,49519?.
Известно , что угол ц? может быть определен по формуле
tg ц? = , где tgл?= .
Подстановка исходных данных даёт
л? = 18, 67669?, tg ц? = или
ц?= arctg 3, 865365 = 75,49516?.
Сравнение результатов расчета показывает на их практическое совпадение.
- ОПРЕДЕЛЕНИЕ НАЛАДОЧНЫХ УГЛОВЫХ РАЗМЕРОВ ДЛЯ ОБРАБОТКИ ВСПОМОГАТЕЛЬНОЙ ЗАДНЕЙ ГРАНИ РЕЗЦА
Искомые наладочные углы б1 поп и ц?1 (рис. 11) находятся аналогичным путем, как и в предыдущем примере. При определении формул следует иметь в ввиду, что для вспомогательной кромки угол наклона л 1 в противоположность углу наклона л главной режущей кромки, считается положительным, если вершина резца занимает наивысшее положение, и отрицательным при низшем ее положении.
При наладке приспособления первый поворот резца выполняется на угол б1 поп (6) вокруг совмещенных осей X и X?. При этом резец поворачивается вместе со своей координатной системой OX?Y?Z? так, что вспомогательная режущая кромка занимает в координатной системе станка OXYZ новое положение, характеризуемое углом ц?1.
Для вывода расчетной формулы по определению угла принимаем рассмотренный выше метод преобразования координат от новой системы OX?Y?Z? к старой OXYZ.
Формулы преобразования координат применительно к данной задаче имеют вид:
Х = Х?. Y = cosб1 поп•Y ?- sinб1 поп•Z ?, где X?=cosл1sinц1; Y?=cosл1cosц1;
Z?= - sinл1.
Искомый угол ц?1 определяется через функцию тангенса: или
. (20)
- ОПРЕДЕЛЕНИЕ НАЛАДОЧНЫХ УГЛОВЫХ РАЗМЕРОВ ДЛЯ ОБРАБОТКИ ГОЛОВКИ РЕЗЦА
Задние грани головки резца и опорные поверхности гнезда под пластину обрабатываются фрезерованием при разных установках и соответствующих наладках приспособления или поворотного стола станка.
Обработка фрезерованием головки корпуса резца с напаянной твердосплавной пластиной (см.рис.6) производится при наладочных углах, вычисляемых по тем же формулам, что и для заточки одноименных граней.

При обработке головки токарного резца с механическим креплением многогранной пластины по вспомогательной задней грани требуется рассмотреть следующее обстоятельство. Чертеж резца для пластины квадратной формы, составленной на основе ГОСТ 26611 - 85 (тип 7) (см. рис. 7), имеет значения углов в плане ц = 750 10 и ц1 = 150. Такие значения углов будут достоверными лишь в том случае, если угол при вершине в плане е = 900. Для пластины квадратной формы это возможно при условии, что опорная поверхность пластины будет параллельна основной плоскости. Однако для образования задних углов режущая пластина наклонена к основной плоскости под углом 50 (рис. 7, сечение А-А). Поэтому угол при вершине в плане на резце будет больше 900 на некоторую величину Д. Тогда вспомогательный угол в плане будет иметь значение ц1 = 1800 - 750 - 900 - Д=150 - Д.
Как было отмечено выше, угол ц1 оказывает влияние на шероховатость обработанной поверхности, прочность вершины резца и другие факторы. Для принятия обоснованного решения при конструировании резца необходимо знать числовое значение величины Д.
Рассмотрим два метода определения величины Д: графический и аналитический. Графический метод обладает хорошей наглядностью, но громоздкий и неточный, аналитический - уступает в наглядности, но значительно выигрывает в точности и трудоемкости.
Графическое решение получено на основе правил проекционного черчения (рис.12). Структура решения задачи та же, что и при наладке двухповоротного приспособления. Необходимо осуществить два независимых поворота резца на углы гпоп и OX”Y”Z” г'пр так, чтобы передняя грань резца заняла положение параллельное плоскости чертежа в неподвижной системе координат OXYZ. На проекции Б - Б и виде А показан поворот режущей кромки относительно оси ОХ на угол гпоп (МВ - исходное положение режущей кромки, М0 В0 - положение после поворота). На проекции в плане по новым координатам X0 Y0Z0 определяется новое положение выбранной на режущей кромки точки М0 и угол ц'. Далее аналогичным образом следует определить поворот резца на угол г'пр .
Аналитический метод построен на основе преобразования координат с помощью матриц вращения. Последовательность преобразования координат от оси OXYZ к системе OX”Y”Z” взята из [10] и приведена в таблице 3.
Таблица 3
Порядок преобразования координат
Переход совершается
|
Ось
перехода
|
Величина перехода
|
Матричная форма записи
|
от системы
|
к системе
|
- OXYZ
- OX'Y'Z'
|
OX'Y'Z' OX''Y''Z''
|
OX'
OY'
|
гпоп
- г'пp
|
X' = A1X
X''= A2X'
|
При выполнении поворота знак угла поворота считается положительным, если поворот совершается от ОХ' к ОY', отOY'к OZ', от OZ' к OX' и т.д.
Формулы преобразования старых координат XYZ в новые X”Y”Z” при двух поворотах подвижной координатной системы последовательно на углы гпоп и - г'пp получим в результате подстановки по графе матричной записи:
X” = A2 · A1X = C · X, где C = A2 · A1
или в подробной записи
Где первый индекс относится к старым осям, а второй - к новым.
Значения промежуточных матриц вращения:
Матрицы вращения перемножают по формуле сik = вi1 а 1k + вi2 а 2k+ вi3 а 3k, т.е. каждый член строки матрицы А2 умножается последовательно на каждый член столбца матрицы А1, а их произведения суммируются, например:
с23 = в21 а 13 + в22 а 23+ в23 а 33 = 0 + sinгпоп+ 0 = sinгпоп.
Члены матрицы произведения имеют значения:
Формулы преобразования координат от системы OXYZ к системе OX”Y”Z” получают вид:
В формулах знаки углов г'пp и гпоп учтены (при определении промежуточных матриц вращения).
Определение угла г” (см. рис. 12,Е).
Исходные данные: координаты точки М(x, y, z).
x = sin 750 = 0,965926 мм; y = - cos 750 = - 0,258819 мм; z = tq150 = 0,087488 мм. (длина проекции ОМ, главной режущей кромки на основную плоскость принята равной l=1мм); углы резца: л = 50; г = - 50; ц = 750; расчетные углы: гпоп = |3,5399740|,
г'пp =|6,1043780|, (см. формулы (2) и (16)).
Подстановка исходных данных в (21), (22), (23) и вычисление дают:
x”= 0,971428мм; y” = - 0,252923 мм; Z” = 0.
Угол ц” определяется по формуле:
.
Подставив численные значения x” и y” в (24), получим ц” = 75,406360.
Определение угла ц1”. Угол ц1” = 900 - ц” = 900 - 75,406360 = 14,593640.
Для определения вспомогательного угла в плане ц1 по вычисленному углу ц1” следует преобразовать координаты точки М1(x”, y”) в координаты точки М1(x, y).
В этом случае порядок обратного преобразования координат от системы OX”Y”Z” к системе OXYZ показан в таблице 4.
Таблица 4
Порядок преобразования координат
Переход совершается
|
Ось
перехода
|
Величина перехода
|
Матричная форма записи
|
от системы
|
к системе
|
- OX''Y''Z'
- OX'Y'Z'
|
OX'Y'Z'' OXYZ
|
OY”
OX'
|
г'пp
- гпоп
|
X' = A X”
X = A X'
|
Формулы преобразования новых координат X”Y”Z” в старые координаты XYZ при двух поворотах подвижной координатной системы последовательно на углы г'пp и - гпоп получим в результате подстановки по графе матричной записи:
где , где матрицы вращения и являются транспонированными по отношению к А1, А2 и С (см. табл. 3). В подробной записи:
где первый индекс относится к новым осям, второй - к старым.
Значения промежуточных матриц вращения:
Матрицы перемножаются по формуле: , т.е. каждый член строки матрицы умножается последовательно на каждый член столбца матрицы , а их произведение суммируются, например:
с32 = а 12 в31 + а22 в32+ а 32 в33 = 0 + 0 - sinгпоп соsг'пp.
Члены матрицы произведения имеют значения:
Формулы преобразования координат от системы OX”Y”Z” к системе OXYZ:
Определение вспомогательного угла в плане ц1. Исходные данные: координаты точки М1 в координатной системе OX”Y”Z”.
X1” = sin 14,593640 = 0,251962 мм;” =cos14,593640 =0,967737 мм; Z1” = 0. (длина отрезка ОМ1 вспомогательной режущей кромки принята равной l = 1 мм); расчетные углы: гпоп = | 3,5399740 |, г'пр = | 6,1043780 |.
Подстановка исходных данных в (25), (26), (27) и вычисление дают:
X1 = 0,250533мм; Y1 =0,964237 мм; Z1 = 0,086496 мм.
Искомый угол ц1 определим по формуле:
.
Подставив численные значения X1 и Y1в (28), получим ц1= 14034?.
Таким образом, отклонение действительного значения угла ц' от значения, поставленного на чертеже, будет:Д = 150 - 14034? = 0026?.
Для обработки вспомогательной задней грани головки резца с механическим креплением многогранной пластины (рис. 7) необходимо знать установочные углы ц1” и б1 поп по следующей схеме.
- В координатной системе OX”Y”Z” (рис. 12) на вспомогательной задней грани зададим три точки М0 (X0”= 0; Y0”= 0; Z0”= 0),
М1 (X1”=sin ц1” ; Y1”= cos ц1”; Z1”= 0) и М2 (X2”= 0; Y2”= 0; Z2”= -1).
- По формулам (25), (26), (27) определим координаты этих точек в системе OXYZ.
- Составим уравнение плоскости, проходящей через заданные тир точки.
- Найдем линию пересечения данной плоскости с координатной плоскостью Х = 0.
- Определим угловой коэффициент k линии пересечения и вычислим б1 поп по формуле:
б1 поп= 90 0 - arctqk (29)
Пример расчета. Вычисление по формулам значения координат точек, в мм:
М1 (X1=0,250533; Y1= 0,964237; Z1= 0,086496); М2 (X2= 0,10634; Y2= 0,061395; Z2= -0,992433); М0 (X0= 0; Y0= 0; Z0= 0). Уравнение плоскости, проведенной через три точки имеет вид:
Вычисление определителя при условиях X0 =Y0= Z0= 0 и Х = 0 приводит к уравнению прямой Z = [(X1Z2 - X2Z1 ) : (X1Y2 - X2Y1 )] Y = kY или Z = Ytqд (рис.13). Искомый угол б1 поп определяется по формуле:
б1 поп= 90 0 - arctq (30)
После подстановки значений координат в (30), получим б1 поп= 20 0.
Угол наклона вспомогательной режущей кромки вычисляется по формуле:
; где X1;Y1; Z1 определяются по формулам (25), (26), (27).
Настройка двух поворотных тисков для заточки резца торцем круга чашечной формы.
Таблица 5.
Продолжение табл.5
Продолжение табл.5
ЛИТЕРАТУРА
- ГОСТ 25751 - 83. Инструменты режущие. Термины и определения общих понятий.
- ГОСТ 25762 - 83. Обработка резанием. Термины, определения и обозначения общих понятий.
- Семенченко И.И., Матюшин В.М., Сахаров Г.Н. Проектирование металлорежущих инструментов. М.: Машгиз, 1953. - 952 с.
- Грановский Г.И., Грановский В.Г. Резание металлов. Учебник для машиностроительных и приборостроительных спец. вузов. - М.: Высшая школа, 1985. - 304 с.
- Родин П.Р. Металлорежущие инструменты. Киев: Вища школа, 1974.- 400 с.
- ГОСТ 26611 - 85. Резцы токарные с механическим креплением многогранных пластин для обработки наружных поверхностей. Конструкция и размеры.
- ГОСТ 26613 - 85. Резцы токарные с механическим креплением многогранных пластин. Технические условия.
- Справочник машиностроителя/ Под ред. Н.С. Ачеркана. М.: Машгиз, 1956. Т. 1. 567 с.
- Режущий инструмент. Лабораторный практикум. Учебное пособие/ Н.Н. Щегольков, Г.Н. Сахаров, О.Б. Арбузов и др.; Под общ. ред. Н.Н. Щеголькова. М.: Машиностроение, 1985. - 168 с., ил.
- Люкшин В.С. Теория винтовых поверхностей в проектировании режущих инструментов. М.: Машиностроение, 1968. - 371 с.
- Металлообрабатывающий твердосплавный инструмент: М 54: Справочник/ В.С. Самойлов, Э.Ф. Эйхманс, В.А. Фальковский и др. М.: Машиностроение, 1988. - 368 с., ил.
|